The melding of advanced embedded control, power electronics, and electric machines has created a new workhorse for industrial and consumer electromechanical energy conversion systems. Electrification will reduce the carbon dioxide output of our economy. Electric motors will replace many other sources of motive power for many industrial purposes. Actively-controlled electric machines are already bringing new profiles for position, speed, and force control, creating consumer products that were previously inconceivable at practical prices.
Electric actuators are increasingly found in just about everything used for daily life, from automobiles to kitchen appliances to smart devices. Modern product design and industrial fabrication demand an understanding of electric machine characteristics, modern control techniques, and associated interactions with electronic drives. Computer-based tools for estimating machine parameters and performance can remarkably speed up a designer's understanding of when different control and machine design assumptions are applicable, and how gracefully these assumptions fail as performance limits are approached. Combinations of motors (electromechanics) and drives (power electronics) can synergistically achieve performance not possible through other means.
This course focuses on the analysis and design of electric motors, generators, and associated power electronic drive systems, placing special emphasis on the design of machines for electric drives, including traction drives, drive motors for automated manufacturing (robots), material handling and drive motors for automotive, aircraft and marine propulsion systems, and associated power electronic drives. Participants will gain extensive hands-on experience by participating in computer-based laboratory exercises in a MATLAB-compatible, open-source scientific analysis tool called Octave. Participants will also engage in a hardware build session using an Infineon “Programmable System on Chip” (PSoC) 5LP to control a machine in our instructional laboratories. The PSoC 5LP is one of a family of processors that can provide sophisticated calculation, reconfigurable hardware, and IoT communication in different applications.
Course exercises will additionally investigate machine performance as affected by design measures such as selection of pole and slot count, winding details, induction machine slot profiles, and optimization of magnets. Computer-based simulation tools will be used to discuss control strategies for different machine types and address optimization techniques, including matching motor design to performance requirements.
Throughout the course, participants will assess performance considerations, trade-offs, and design approaches and access computer facilities and analysis routines for practice in machine analysis and design. Hardware experience will include building and programming a small, motor drive using a processor from a family of IoT-capable programmable controllers.
COVID-19 Updates
We fully expect to resume on-campus Short Programs courses during the Summer of 2022. However, the possibility remains of ongoing disruption and restrictions due to COVID-19 which may require that the course be delivered via live virtual format. Please read more here.
Certificate of Completion from MIT Professional Education
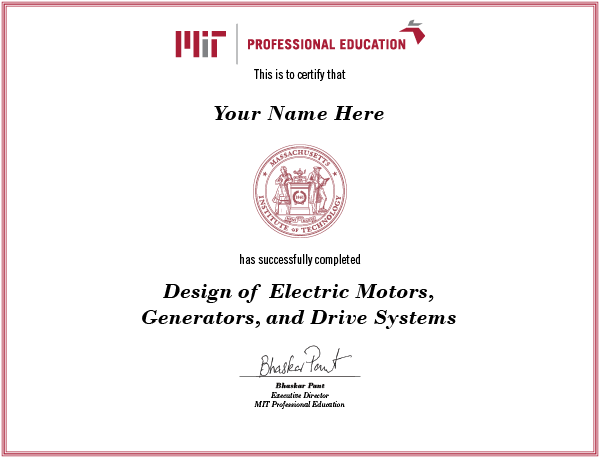